Common Failures in LOLER Examinations and How to Prevent Them
- Helen Thomas-O'Brien
- May 29, 2024
- 3 min read
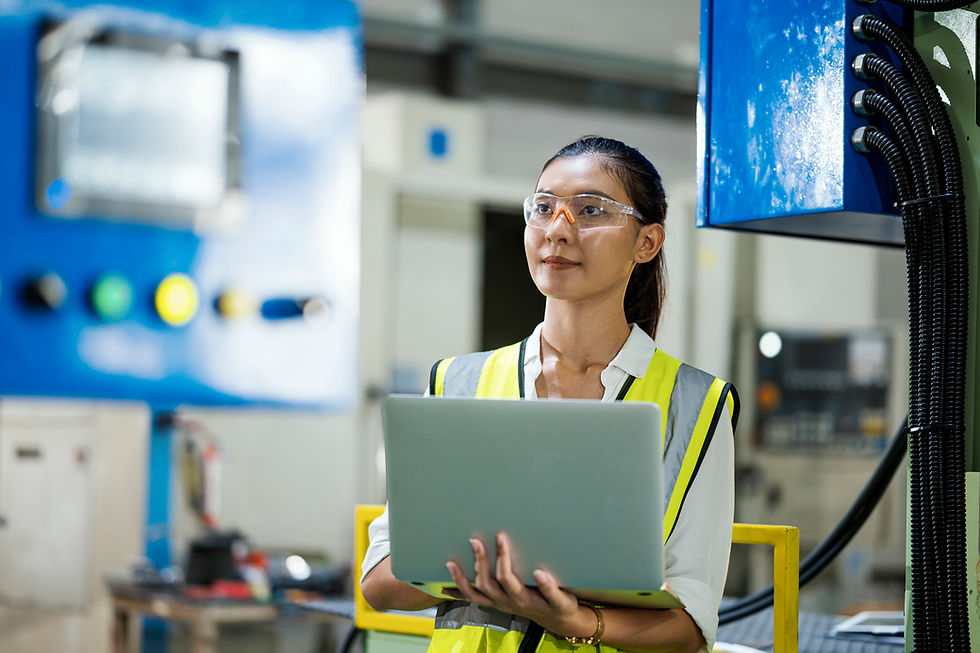
Ensuring the safety and compliance of lifting equipment is a critical responsibility for any organization. The Lifting Operations and Lifting Equipment Regulations (LOLER) require regular inspections to identify potential hazards and ensure that lifting equipment is safe to use. However, many organizations encounter common failures during LOLER examinations that can compromise safety and compliance. In this blog post, we’ll explore the most common failures found during LOLER examinations and provide practical tips on how to prevent them.
Importance of LOLER Examinations
LOLER examinations are essential for several reasons:
Safety: Identifying and addressing potential hazards can prevent accidents and injuries.
Compliance: Adhering to LOLER regulations is a legal requirement in the UK. Non-compliance can result in severe penalties.
Operational Efficiency: Well-maintained lifting equipment reduces the risk of breakdowns, ensuring smooth and uninterrupted operations.
Insurance: Compliance with LOLER regulations is often a prerequisite for insurance coverage. Regular inspections help avoid disputes in the event of an accident.
Common Failures in LOLER Examinations
Worn or Damaged Lifting Chains and Slings
Issue: Lifting chains and slings can become worn or damaged due to heavy use, overloading, or improper handling.
Impact: Worn or damaged chains and slings can fail during lifting operations, leading to dropped loads and potential injuries.
Prevention: Regularly inspect all lifting chains and slings for signs of wear, corrosion, or damage. Replace any components that show signs of deterioration. Ensure proper storage and handling to prolong their lifespan.
Faulty or Inadequate Safety Devices
Issue: Safety devices such as overload indicators, limit switches, and emergency stop buttons may be faulty or inadequately maintained.
Impact: Faulty safety devices can fail to prevent accidents, putting operators and bystanders at risk.
Prevention: Test all safety devices regularly to ensure they are functioning correctly. Schedule routine maintenance and promptly repair or replace any faulty components.
Improperly Maintained Lifting Equipment
Issue: Lack of regular maintenance can lead to mechanical failures, including issues with gears, motors, and other critical components.
Impact: Poorly maintained equipment can malfunction during use, causing accidents and downtime.
Prevention: Follow the manufacturer’s maintenance guidelines and schedules. Keep detailed maintenance records and ensure that all maintenance tasks are performed by qualified personnel.
Incorrectly Installed or Modified Equipment
Issue: Equipment that is incorrectly installed or modified without proper assessment can pose significant safety risks.
Impact: Incorrect installation or unauthorized modifications can lead to equipment failure and accidents.
Prevention: Ensure that all lifting equipment is installed and modified by qualified technicians. Conduct thorough inspections after any installation or modification to verify compliance with LOLER regulations.
Lack of Proper Documentation
Issue: Incomplete or missing documentation, including inspection records and maintenance logs, can hinder the ability to track equipment condition and history.
Impact: Lack of proper documentation can result in missed inspections and overlooked maintenance tasks, increasing the risk of equipment failure.
Prevention: Maintain detailed and up-to-date records of all inspections, maintenance, and repairs. Use a systematic approach to document and track the condition of all lifting equipment.
Operator Errors
Issue: Operators who are not adequately trained or who do not follow proper procedures can contribute to equipment failures.
Impact: Operator errors can lead to accidents, equipment damage, and non-compliance with LOLER regulations.
Prevention: Provide comprehensive training for all operators on the correct use and maintenance of lifting equipment. Regularly review and reinforce safety procedures and best practices.
Overloading of Lifting Equipment
Issue: Exceeding the maximum load capacity of lifting equipment can cause severe damage and increase the risk of failure.
Impact: Overloading can result in dropped loads, equipment damage, and accidents.
Prevention: Always adhere to the manufacturer’s specified load limits. Use load indicators and ensure that operators are trained to recognize and avoid overloading.
How OR Group LTD Can Help
At OR Group LTD, we specialize in conducting thorough LOLER examinations to ensure your lifting equipment is safe and compliant. Our comprehensive inspection process includes:
Initial Assessment: Reviewing maintenance records and previous inspection reports.
Visual Inspection: Identifying signs of wear, damage, or defects.
Functional Testing: Assessing the performance of the equipment under normal operating conditions.
Load Testing: Verifying that the equipment can handle its maximum rated load safely.
Detailed Reporting: Providing a comprehensive report detailing our findings and recommendations.
Compliance Certification: Issuing a LOLER compliance certificate once the equipment passes the inspection.
Conclusion
Understanding and preventing common failures in LOLER examinations is crucial for maintaining a safe and compliant workplace. By implementing regular inspections, adhering to maintenance schedules, and ensuring proper operator training, you can significantly reduce the risk of equipment failures. Remember, OR Group LTD is here to assist with all your LOLER inspection needs, ensuring your lifting equipment remains in optimal condition.
For more information or to schedule a LOLER inspection, contact us today at 0330 043 4773 or visit our website at www.orgroupltd.com.
Stay safe, stay compliant.
コメント